Colchester Storm VL-1000 with Integrated Meltio 3D Printing
Hybrid CNC Machining Center with Additive Manufacturing for Advanced Metal Processing
The Storm VL-1000 is a powerful vertical machining center from Colchester, now available with an integrated Meltio Engine for hybrid manufacturing. This combination enables both traditional CNC machining and advanced metal 3D printing in a single machine.
By integrating the Meltio Engine into the Storm VL-1000, you gain a flexible solution for producing complex components, repairing worn-out parts, and modifying existing workpieces. The system supports both Meltio IR and Meltio Blue laser heads, offering material versatility for a wide range of applications.
Key Specifications – Storm VL-1000:
- Travel (X, Y, Z): 1020 x 510 x 560 mm
- Spindle Speed: 10,000 RPM, BT40 taper
- Table Size: 1200 x 500 mm, max load 800 kg
- Rapid Traverse (X, Y, Z): 36 m/min
- Tool Magazine: 24-position twin-arm type
- Machine Weight: 5190 kg
Meltio Engine – Integrated Metal 3D Printing:
- Laser-based Directed Energy Deposition (DED) technology
- Material compatibility: Stainless steel, tool steel, titanium, Inconel, copper, aluminum, and more
- Ability to combine multiple materials in a single part
- High material efficiency – minimal waste
- Available with IR or Blue laser head for customized applications
Benefits of Hybrid Manufacturing:
✅ Machine and print in a single operation – save time and reduce post-processing
✅ Flexible material choices – use standard metal wire for cost-effective production
✅ Repair and modify components – extend the lifespan of critical parts
✅ Combine subtractive and additive manufacturing for unique design possibilities
This solution is ideal for workshops, industrial manufacturers, and R&D environments looking to merge machining and metal printing into one powerful system.
Roller Type Linear Guide Ways
The Linear Motion Guideways feature low friction and free from stick-and-slip problems. Such the characteristics are especially suitable for high speed 3D cutting and finishing. The quality of workpiece surface is increased and the need for manual polishing of workpiece surfaces is reduced.
Machine Specification
Control Fanuc Oi-MF with Manual Guide i
Siemens 828D with ShopMill
Travels
X, Y, Z (mm) 1020 x 510 x 560
Spindle nose to Table (mm) 150-710
Table
Working Area (mm) 1200 x 500
Max Load (kg) 800
T-Slots (No. x Width x Pitch) 5 x 18 x 100
Spindle
Spindle Taper BT40
Speed (rpm) 10,000 Belt Drive with Oil Cooler
Spindle Motor (Kw) Fanuc (7.5/11Kw)
Siemens (9Kw)
Feed Rates
Rapid Traverse X, Y, Z (m/min) 36
Max Cutting Feedrate (m/min) 10
Tool magazine
ATC 24 Station Twin Arm
Type BT40
Max Tool Diameter (mm) 80
Max Tool Weight (kg) 7
Max Tool Length (mm) 300
Dimensions
Net Weight (Kg) 5190
Power Requirement (Kva) 15
Floor Space (L x W x H) 2980 x 2955 x 3045mm
Standard Accessories
Screw Type Chip Auger and Cart
Spindle Air Blast
Coolant and Air Gun
Heat Exchanger
Spindle Oil Cooler
Portable MPG
LED Light
Coolant System
Cycle Indicator Light
Levelling Pads
CE
4th Axis Preparation
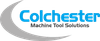
Colchester
Why Colchester Machine Tool Solutions?
- An installed base of over 100,000 Colchester and Harrison lathes worldwide
- All products from Colchester, Harrison, Pratt Burnerd, Clausing and Gamet are designed and manufactured to exceed the highest international quality and safety standards
- Stock machines and workholding available quickly
- Experienced, factory trained engineers and support staff offering speedy response to your needs
- Backed up by over £4 million of genuine manufactured spare parts
- The number one choice for industry and education globally