Meltio Engine CNC Integration
Hybrid Manufacturing Solution
The most affordable hybrid manufacturing solution, fitting almost any CNC machine on the market. Enable metal 3D printing and machining of complex geometries in a single process step.
The Meltio Engine is the ideal CNC complement for near-net shape manufacturing, repair and feature addition.
Hybrid Manufacturing
Create highly complex parts with machining tolerances in the same process.
Part Repair
Cost-effective component repair, part augmentation, and feature addition.
Retrofitting
Provide new capability to any CNC machine by turning it into an hybrid metal manufacturing system.
Geometry Freedom
No inherent constraints when the working envelope is only limited by the size of the motion system.
Meltio CNC Applications
Watch Bezels
Titanium 64
Size:
50 x 45.9 x 12.7 mm
Weight:
0.25 kg
Print Cost:
$ 40
Elbow
SS316L
Size:
ext. 70 Ø – int. 50 Ø mm
Weight:
0.51 kg
Production Time:
6 h
Gas Turbine Blade Repair
Nickel 625
Size:
65 x 29 x 6 mm
Weight:
0.015 kg
Print Cost:
$ 1.55
https://meltio3d.com/metal-3d-printers/meltio-engine-cnc-integration/
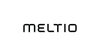
Meltio takes metal additive manufacturing to the next level by developing and manufacturing high-performance, affordable, and easy-to-use metal 3D printing solutions using wire-laser metal deposition (LMD) technology.
Meltio, founded in 2019 and based in Linares (Spain), develops and fabricates high-quality disruptive products aimed at high-profile industrial end customers and R&D organizations, such as universities and research-oriented companies.
The current portfolio of metal solutions includes the Meltio M450 metal 3D printer, the Meltio Engine CNC Integration, which turns virtually any CNC machine into a powerful hybrid manufacturing center, and the Meltio Engine Robot Integration, which is the perfect platform for large and complex 3D printing, repair, cladding, and feature addition.
The company’s latest product launch, Meltio Robot Cell is an affordable turn-key solution for the Meltio Engine Robot Integration. All of the systems share the same patented LMD-based (a type of Directed Energy Deposition (DED) process) process capable of manufacturing parts using commodity welding wire.